開発ストーリー
若手中心のチーム編成で
妥協なき開発を推進。
「働き方をも変える機械」は、
こうして生まれた。
2021年10月1日にラチスブームクローラクレーン
「マスターテック7200G NEO」が販売開始された。
その開発背景には、高度な操作技術が求められるクレーンの安全性やパワー、
操作性などへの要求がより高まっていることがある。
それらは、仕上がりや工期、コストなどとともに、
現場の第一線で働く人たちの快適さや、働きやすさに直結する課題だ。
ここでは、こうした課題を解決する「マスターテック7200G NEO」の
誕生秘話や想いをテーマに、座談会を実施。
若手中心で編成した開発部門とマーケティング・サービス・営業部門の
それぞれの立場から語ってもらった。
STORY 01:開発部門 編
-
浦 真也
技術開発本部
クレーン開発部
クレーン開発グループ
シニアマネージャー2005年入社。海外向けラフテレーンの開発を担当した後、ラチスブームクローラクレーンのキャブ開発やカスタム設計に従事。17年より、本開発に携わる。プロジェクトマネージャーとして開発方針の決定から営業部門・製造部門を含めた全社の意思統一などプロジェクト全体を牽引した。
-
松本 宗馬
技術開発本部
開発試験部
クレーン試作試験グループ2014年入社。開発試験室でクローラクレーンの試験スタッフを経て、クローラクレーンとフィールド不具合原因究明や対策効果確認の試験に携わる 。本開発では、開発を円滑に進めるために試験日程調整や試験の遂行および評価を実施した。
-
高岡 大輔
技術開発本部
クレーン開発部
クレーンアタッチ
開発グループ チーフ2007年入社。大型機のアタッチメント関連の開発を担当。本開発でも、アタッチメントの新機種開発業務を担当し、アタッチメント全般の取りまとめ、設計に従事した。
-
牟田 学史
技術開発本部
クレーン開発部
クレーン開発グループ
アシスタントマネージャー2005年より、鈑金部品サプライヤの設計者として、祇園工場にてショベルガード設計に従事。09年に大久保工場に移り、Gシリーズ全般のクレーンガード開発を担当。17年からは今回の「デライトキャブ」の開発に着手した。コンセプト立案からインテリア設計、デザインを担当。
-
寺西 賢太郎
技術開発本部
システム・コンポーネント開発部
クレーン統合システム
開発グループ2012年入社。広島事業所でショベルの電装設計業務を手がけた後、大久保事業所でクレーンの電気システム設計を担当。本開発では、クレーンの新制御開発、新機種向けソフトウェアの開発に従事した。
-
有田 隆一
技術開発本部
クレーン開発部
クレーン開発グループ
マネージャー2008年入社。生産技術室、製造室にて機械加工を担当後、14年より構造強度技術グループへ。17年からは半年間、東日本営業グループに異動。その後は開発部門に戻り7200G NEOの本体構造物の設計と、機械全体の機能の設計開発に携わった。
市場の声で機能を
つくり込んでいく
ベクトルを堅持
- 浦:
- 「マスターテック7200G」のフルモデルチェンジを進めた今回の開発は、「すべてのお客様に使いやすいマシン」を目指して、クレーンに求められる機能や、今までの商品のどこに改善点があるのかといった、ユーザの生の声を収集する最上流のプロセスに、従来以上に時間をかけました。そこから得られたものを丁寧に選別し、開発要件としてプロジェクトで具現化する活動にも多くの時間を割きました。
- 有田:
- 私たち開発部隊も、実際のお客様を訪問するなかで、「まだ誰もやっていないことを実現しよう」という気持ちが膨らんでいきました。
- 高岡:
- クレーン・アタッチメントの強度とつり上げ能力には相関関係があります。その一方で、安定性を巡る剛性と軽量化は、大きな相反課題でした。そこで新規構造のアタッチメントは、製造工程での製作性を考慮して、先行開発を進めました。
- 寺西:
- 若手はもちろん、ベテランにとっても「タワー立ち上げは最も気を使う作業だ」というオペレータさんの声が多かったんです。今回、ワンレバーでブームアップと格納を実現する「タワー自立アシスト」が、そんな悩みを解決してくれます。これは胸を張って自慢したいですね。
- 牟田:
- 「デライトキャブ」と名付けた運転席は、視界性や操作性などはもちろん、マシンの全体的なフォルム・イメージを決定づけるデザイン性にも気を配りました。
- 松本:
- 試作段階では、若手でも乗りやすく、ベテランはさらに腕が発揮できる、そんなユニバーサル思想の実現と、優れた機能性や高い安全性が発揮できているかを、皆さんの開発成果に対して厳しい視点でチェックしました。
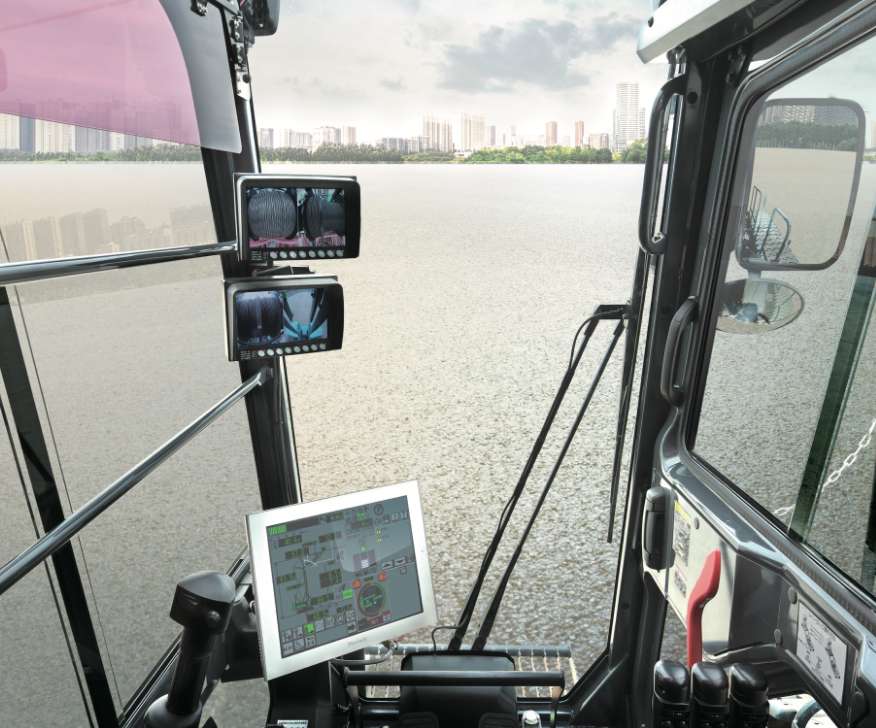
デライトキャブからの視界。
足下から頭上まで、視界を遮ることなく広い視野が開ける。
細部にも気を配る
設計姿勢を徹底
- 浦:
- 30t以下に分解するため、主・補ウインチを本体ではなく下部ブームに搭載したレイアウトとし、ワイヤロープを仕込んだままでも輸送できる構造を採用しました。「輸送しやすく、組立・分解しやすいマシンに」という要望にも、十分応えられたと思います。
- 牟田:
- デライトキャブは、ワイパモータを下方に設置したり、作業の死角を生むフロントと天井ガラス間のピラーを撤廃したり、さらに左窓の大型化などで全方向への視界を拡大しました。開放的な視界の広さを実感していただけるはずです。
- 有田:
- 「メンテナンスアプローチのしやすさ」のニーズも高いことが判明しました。そこで、バッテリやフィルタ類も手前から簡単に確認や交換ができ、グリスアップなども、集中ポイントへの給油で各部に届く構造を工夫しました。油圧の電気化でキャブ後部に防水電気室を設けて保守性も格段に向上させています。
- 寺西:
- メンテナンス面でいえば、オイル交換のタイミングがアラートとともにモニタ表示され、遠隔からでもWeb上で確認ができるようになりました。組立用リモコンもワイヤレスにしたことで、ピン挿入や旋回、ブーム起伏なども最適な場所から、直接目視しながら実行できます
- 高岡:
- ブームは風のあおり・軽量化強度解析を徹底し、足場を従来の400mm×1列から500mm×2列へと広く改良しながら、「より強く、より軽く」を実現しました。
- 松本:
- 各部のこだわりや設計理念、解析結果を実機上で検証したのですが、トライ&エラーを繰り返すことで、ユーザ本位のカスタマイズ性の高さを実現できました。
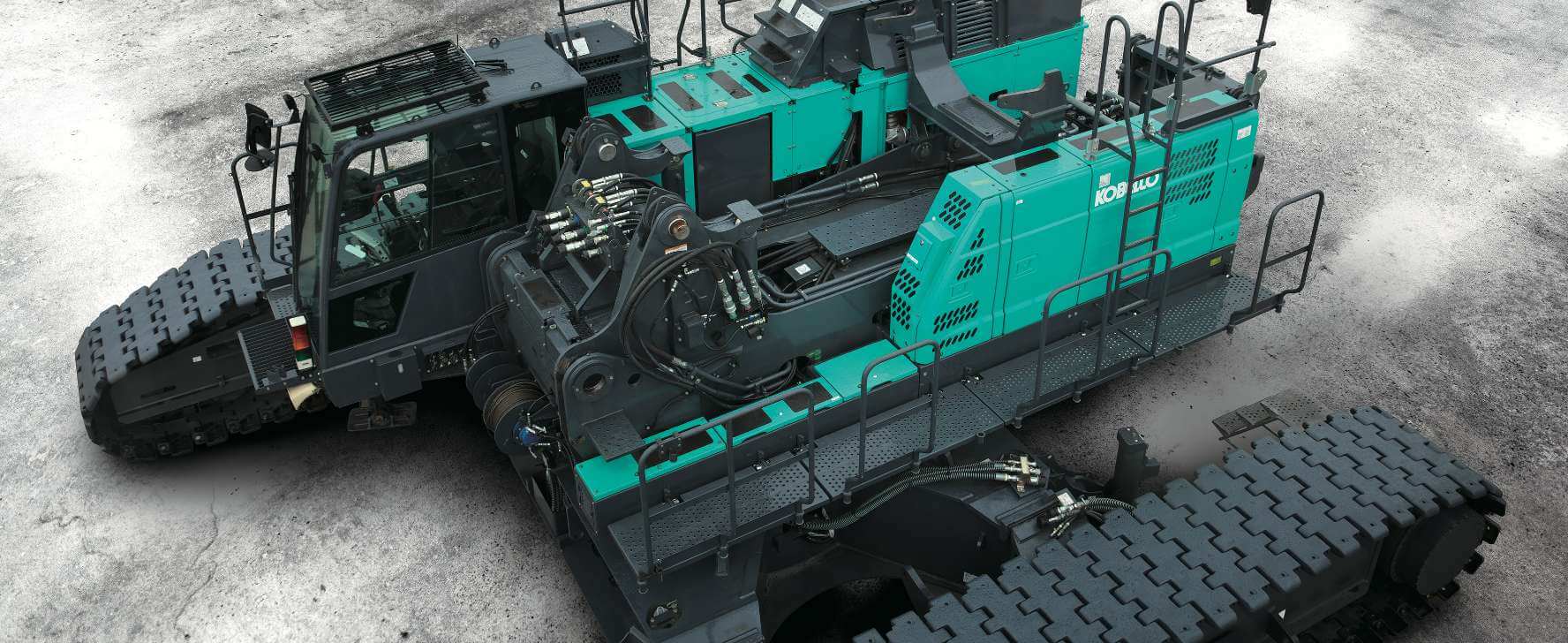
下部ブーム、ガントリを外すと、すべてのウインチが本体から外れるウインチレスボディ。輸送効率が飛躍的に向上。
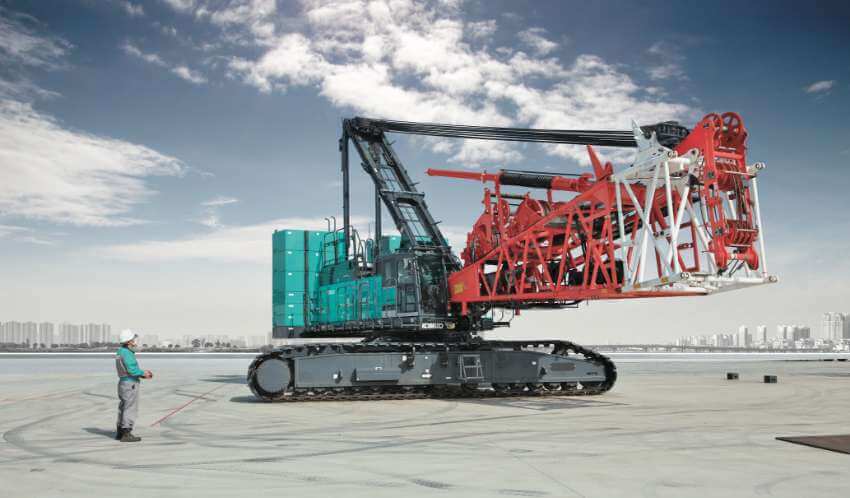
遠隔で位置を確かめながら安全操作を実現する組立用ワイヤレスリモコン。
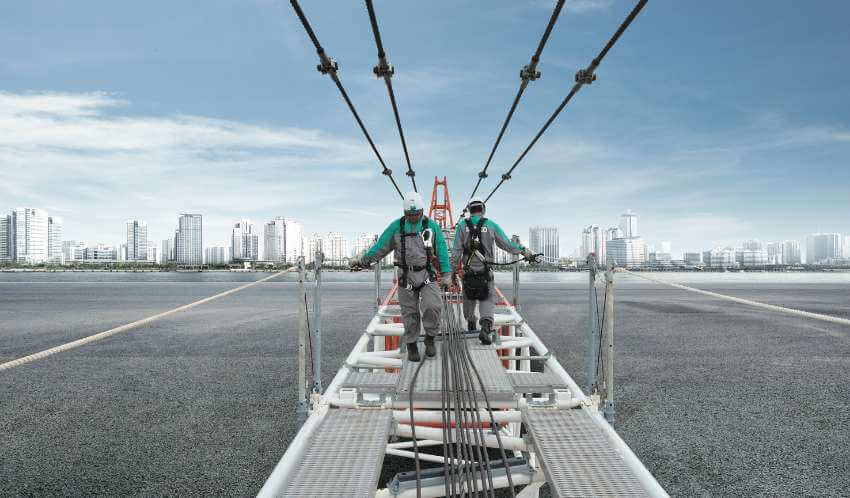
ブーム上面足場は、500mm×2列。中間ブームの上面足場は、1,000mmに拡大。
完成度の高さを
達成感とともに再認識
- 高岡:
- 事前ヒアリングや構想期間で理想型を突き詰めていった姿勢も功を奏し、まさにフルモデルチェンジと呼ぶにふさわしい製品になったと思っています。
- 有田:
- 分解も楽で、輸送段階から大きくアップした機動性を実感してほしいですね。
- 松本:
- まさに「乗って楽しいマシン」に仕上がっています。多くの方に試乗していただき、この成果を体感してもらいたいですね。
- 牟田:
- デライトキャブにおける、操作視界の広さも、そんな「楽しさ」を生み出すことに貢献できたと自負しています。
- 寺西:
- オペレータの方々を支援するさまざまな工夫も、必ず驚きをもって感じていただけるはずです。
- 浦:
- 今回、若手を中心に開発チームを編成し、7200G NEOの開発に取り組みました。開発途中で課題に直面した時は、解決に向けて多方面からサポートをいただき「全員で力を出してやりきった」感があります。この取り組み方は今後新たなクレーンを開発する際のスタンダードになると確信しています。
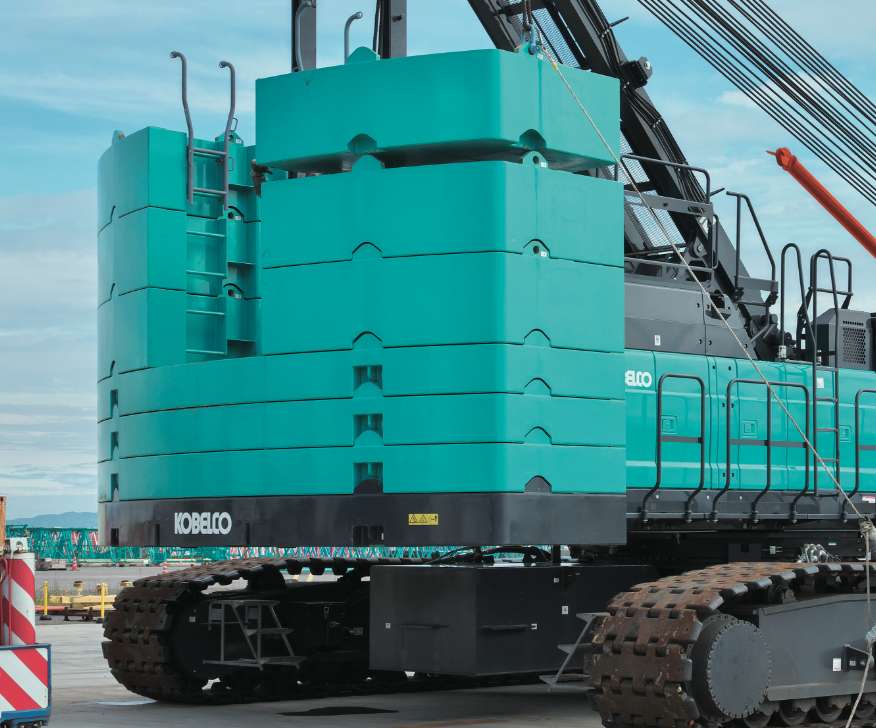
位置合わせしやすいカウンタウエイトは、グループごとに形状を共通化。輸送性・組立性に配慮した設計を追求。
-
開発ストーリー
若手中心のチーム編成で妥協なき開発を推進。
「働き方をも変える機械」は、こうして生まれた -
フルモデルチェンジした
マスターテック7200G NEO
開発部 部長が語る本開発の全体像 -
マスターテック7200G NEO
解剖図